Industry Page 3
traffic,biomedicine,mechanical,and CG softs.
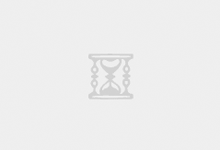
Hexagon RADAN 2025.1 introduces powerful enhancements that streamline operations, improve part traceability, and deliver measurable savings on time and cost. With improved automation, better feedback in error handling, and tighter integration across the suite, RADAN 2025.1 continues to drive productivity in sheet metal fabrication. Available other versions: 2024.1 ,2021.0 Hexagon SMIRT 2025.1 Tested Picture Part Marking You can now use rectangular Data Matrix codes instead of square ones, helping you cut down marking time and consumable use by up to 30%. Tooling Hints Tooling errors are now much easier to deal with—just click on any item in the list, and RADAN will instantly zoom in to show you exactly where the problem is. Import Parts Adding parts to your project...
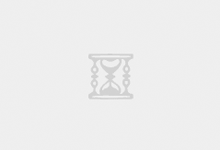
Sima software is for efficient analysis of complex multi-body systems, including mooring analysis and marine operations. Coupled analysis of marine systems, including mooring analysis Are you looking for in-place analysis or marine operations software that can do coupled analysis of any type of floating structure, including offshore wind turbines? The Sesam module Sima can perform analysis, including the coupled effect of waves, wind and current for structural analysis or mooring analysis. Available other versions: 4.8x , 4.6x DNV Sima 2024 v4.8 Tested Picture For many floating structures, the combined effects of wind, current and waves must be taken into account. When this is to be applied to complex, multi-body systems, very efficient calculations are needed. Sima computations are based on the well-known...
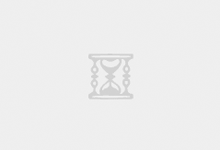
Body Manufacturing-Stamp (BM-Stamp) from ESI is a cost-attractive simulation solution that empowers automotive part manufacturers to optimize their stamping processes, reducing the reliance on physical prototypes, and improving the precision and quality of manufactured parts from early on in their project lifecycle. BM-Stamp provides an extremely easy-to-use graphical interface enabling precise stamping validation for all automotive materials without requiring engineers to have FEM or other numerical expertise, enabling highly predictive formability, accuracy, and aesthetic results in a consistent manner. ESI BM-STAMP 2025.0 Tested Picture Recognized as a trusted engineering partner, ESI delivers precise validation for engineers to consistently achieve top simulation results, and as a consequence reduce overall costs, and accelerate production timelines. Key Values Delivered by BM-Stamp Minimize Cost...
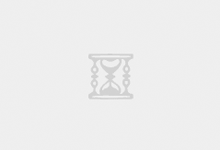
ESI PAM-STAMP is a trusted sheet metal forming solution with over 25 years of proven use across aerospace, white goods, heavy machinery, and electronics industries. The solution includes a high degree of flexibility which allows to tackle sheet metal formability challenges across advanced and flexible processes—all within a single environment. From part and tooling design phase to production, PAM-STAMP enables you to virtually develop and validate almost any sheet metal forming process and the setup and analysis of automotive hemming processes. ESI PAM-STAMP 2025.0 Tested Picture The solution offers simple-to-use, dedicated process templates, and workflows for most sheet metal forming processes, for example, tube-bending, hydroforming, and flex forming, allowing even engineers with limited experience to produce high-quality simulation outcomes. Thanks...
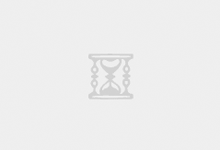
Monarch is a market leading desktop-based self-service data preparation solution. Monarch connects to multiple data sources including structured and unstructured data, cloud-based data, and big data. Connecting to data, cleansing and manipulating data requires no coding. Available other versions: 2024.0 , 2023.0 Altair Monarch 2025.0 Tested Picture Monarch can quickly convert disparate data formats into rows and columns for use in data analytics. Over 80 pre-built data preparation functions mean data preparation tasks can be completed quickly and error free. More time is spent on generating value from data as opposed to making data usable to begin with.
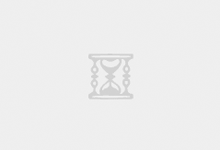
VPIdeviceDesigner™ is a versatile simulation framework for the analysis and optimization of integrated photonic devices, waveguides, and optical fibers. Available other versions: 2.7 , 2.6 VPIphotonics VPIdeviceDesigner 2024 v2.7 Tested Picture This powerful design tool offers a set of full-vectorial finite-difference mode solvers for waveguide analysis as well as a beam propagation method (BPM) and an eigenmode expansion method (EME) for simulating 2D and 3D photonic devices. VPIdeviceDesigner supports the flexible definition of 2D waveguide cross-sections and 3D device layouts with realistic (dispersive, temperature-dependent, etc.) optical materials, widely customizable nonuniform meshing, and perfectly matched layers. VPIdeviceDesigner provides a user-friendly object-oriented Python interface, which is closely integrated with the Python-based ecosystem of open-source software for mathematics, science, and engineering, including the...
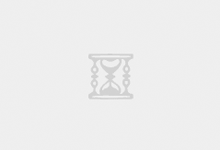
VPIphotonics Design Suite comprises professional application-specific simulation tools and add-on toolkits for photonic components and optical transmission systems. They provide flexible usability functions, versatile analysis capabilities, and custom design process support tailored for day-to-day engineering and leading-edge research.It include plugin VPItoolkit ML Framework,VPItoolkit PDK DemoFab and VPItoolkit QKD. Version 11.6 significantly advances simulation and design flows for many applications, including computing, datacenter interconnects, laser satcom, and high-capacity core networks. Available other versions: 11.5 , 11.4 , 11.3 VPIphotonics Design Suite 2025 v11.6 Tested Picture Among the new Modeling Capabilities of version 11.6 are Enhanced BER 4D module to support mismatched decoding using a multivariate Gaussian auxiliary channel model, enabling more realistic calculation of MI, GMI, and LLRs in coherent systems...
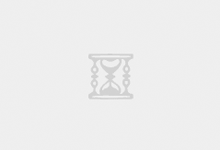
Materialise Mimics Core is a 3D medical image segmentation software,Move from 3D medical image data to 3D modeling efficiently and accurately. Mimics Core’s unmatched virtual procedure planning capabilities allow you to manage even the most uncommon patient cases and challenging image data. Available other versions: Materialise Mimics Core 27.0 with 3-Matic Medical 19.0 , Materialise Mimics 26.0 with 3-Matic Medical 18.0 Materialise Mimics Core 27.1 with 3-Matic Medical 19.1 Tested Picture Features Effective anatomy segmentation Combine AI-enabled automated tools with smart editing tools to obtain accurate 3D models. Accurate anatomy analysis Identify landmarks and analyze the anatomy with an extensive set of 3D measurement tools. Virtual procedure planning Visualize different procedure scenarios for improved understanding. Virtually position devices to fully...
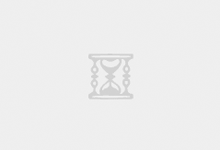
3-matic enables you to clean up rough data from a CAD design, topology-optimized model, simulation, or scanned data by making design modifications on the mesh level. Enhance models for 3D printing with 3D textures, lattice structures, conformal structures, and scripting automation to easily create ranges of validation samples — improving your overall productivity. Available other versions: 19.0 , 18.0 Materialise 3-matic 19.0 Tested Picture Benefits Freedom of design With 3-matic, you can fully personalize your products and create models that are impossible to produce with traditional manufacturing methods. Save time and costs Leverage 3-matic’s tools and the Lattice Module to create designs that outperform solid parts and require less material, reducing costs and printing time. Features Post-topology optimization tools Redesign...
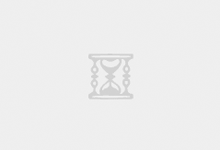
PC-DMIS 2025.1 is ready for the future of metrology with full support for Hexagon’s next generation CMMs – the groundbreaking Maestro and ATS800 Tracker. Available other versions: 2024.1 , 2023.2 Hexagon PC-DMIS 2025.1 Tested Picture Whether you’re working with bridge, horizontal, portable arms or trackers, PC-DMIS is the one metrology software that is compatible with all types of Hexagon CMM. PC-DMIS 2025.1 is ready for action with Hexagon’s latest generation of metrology devices – the groundbreaking Maestro CMM and the new ATS800 Tracker. Reduce the learning curve and increase valuable inspection time with the metrology software that can do it all. Features and Key Improvements in PC-DMIS 2025.1 PC-DMIS support for Maestro CMM PC-DMIS is ready for use with Maestro...