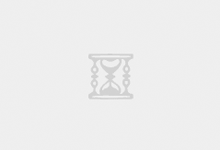
Oasys 22.0 is the latest release of the comprehensive Ansys LS-DYNA pre- and post-processing software environment. This version further strengthens the suites’ leading position in the market by offering flexibility, speed, performance, and efficient end-to-end workflows for human-safe design, and much more. Advancements include support for C-NCAP and usability improvements for Virtual Testing, Injury Metrics, new IGA (Isogeometric Analysis) and CPG (Continuum Particle Gas) features, Connections and Load Path tool enhancements. Version 22.0 enables users to achieve even greater automation and process integration, resulting in significant workflow efficiency and excellent model quality and results. Available other versions: 21.x , 20x , 19.x , 18.x Oasys Suite(PRIMER\D3PLOT\T/HIS\REPORTER\SHELL) 2025 v22.0 Win/Linux64 Tested Picture Efficient end-to-end workflows Virtual testing Virtual Testing capabilities have...
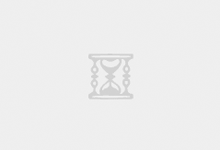
3-matic enables you to clean up rough data from a CAD design, topology-optimized model, simulation, or scanned data by making design modifications on the mesh level. Enhance models for 3D printing with 3D textures, lattice structures, conformal structures, and scripting automation to easily create ranges of validation samples — improving your overall productivity. Available other versions: 19.0 , 18.0 Materialise 3-matic 19.0 Tested Picture Benefits Freedom of design With 3-matic, you can fully personalize your products and create models that are impossible to produce with traditional manufacturing methods. Save time and costs Leverage 3-matic’s tools and the Lattice Module to create designs that outperform solid parts and require less material, reducing costs and printing time. Features Post-topology optimization tools Redesign...
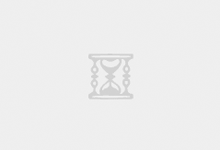
AtaiTec SI Suite 2025 is a signal integrity tools – ISD, ADK, X2D2 and MPX – were developed by SI engineers for SI engineers. These tools reduce tedious SI tasks including field solver simulation, circuit simulation, channel simulation, de-embedding and correlation with VNA/TDR measurements, to only a few mouse clicks. Available other versions: 2024.07-2024.11 AtaiTec SI Suite 2025.04 Tested Picture We specialize in signal and power integrity modeling, simulation, and measurement correlation for IC, package, connector, cable, and board. Our mobile-app-like SI software complements your 3D full-wave field solver, circuit simulator and VNA, and helps correlate simulation and measurement results: In-Situ De-embedding (ISD) replaces TRL calibration and helps save hardware cost. Advanced SI Design Kit (ADK), a...
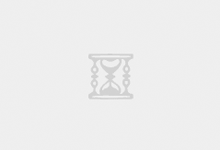
Knowledge Studio is a market-leading easy to use machine learning and predictive analytics solution that rapidly visualizes data as it quickly generates explainable results – without requiring a single line of code. Available other versions: 2023.3 Altair Knowledge Studio 2025.1 Tested Picture A recognized analytics leader, Knowledge Studio brings transparency and automation to machine learning with features such as AutoML and Explainable AI without restricting how models are configured and tuned, giving you control over model building. Key Features No Code Machine Learning Modeling An interactive and intuitive interface allows users of different skill sets to quickly connect to a wide range of data sources, transform disparate data formats into usable datasets, and generate insights by using a wide range...
Ansys cloud-native solutions provide unparalleled capacity to speed up completion times for even the largest finFET integrated circuits (IC) and 3D/2.5D multi-die systems. These powerful multiphysics analysis and verification tools reduce power consumption, improve performance and reliability, and lower project risk with foundry-certified golden signoff verification. Features Power integrity (EM/IR) analysis and modeling with RedHawk-SC for digital, and Totem-SC for analog designs Electrothermal analysis of 2.5D/3D multi-die systems Variability-aware path timing with Path FX Electrostatic discharge (ESD) and reliability analysis with PathFinder-SC RTL power analysis and reduction with PowerArtist On-silicon electromagnetic analysis and modeling with RaptorH, Pharos, Exalto, and VeloceRF Cloud-native elastic compute architecture for full-chip capacity
MVTec HALCON 24.11, we are focusing on even better AI, specifically deep learning algorithms. Among other features, users can now detect and evaluate unexpected behavior in deep-learning-based classification. Out of Distribution Detection (OOD) for Classification This new HALCON feature makes it easy to recognize unexpected behavior caused by incorrect classifications in production. Thus, users can take appropriate measures, such as stopping the machine, in a targeted and efficient manner. When using a deep learning classifier, unknown objects are assigned to one of the classes that the system has learned. This can lead to problems if, for example, the defects or objects themselves are of a type that has never occurred before. The new deep learning feature “Out of Distribution Detection...
Vortex® Studio serves as a platform for developing and launching real-time, interactive simulations of mechanical systems. It constitutes a vital element in all of CM Labs’ top-tier equipment simulation training packs and can be used for designing and producing personalized real-time, interactive simulation products. Vortex Studio comprises two packages : Vortex Create : visually build real-time mechanical machines and scenarios. Vortex Activate : deploy content created in systems ranging from desktop to many-screen custom simulators. Vortex Create Key Features Visual Editor allows to build visually high-fidelity real-time mechanical systems. High-fidelity physics engine with a number of extension modules including : Rigid Body Vehicle, Tire, and Track Models Cables Earth-Moving Allows users to simply extend the core functionalities using Python 3 scripting. Verification...
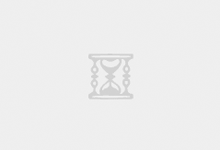
Synopsys S-Metro provides a comprehensive and powerful toolbox for automated assessment of numerical and image-based metrology data for photomask qualification, modeling data preparation, and process characterization. Process engineers use it to measure the lithographic performance, for instance through process window analysis. Synopsys S-Metro 2024.06 Win/Linux64 Tested Picture Metrology images from any source, whether photomask or wafer, can be processed and analyzed in Synopsys S-Metro as well. Images are aligned to the corresponding layout and can be averaged to improve contrast; contours are extracted for use in model calibration and validation as well as for training machine learning modes. Synopsys S-Metro automatically processes SEM image and CD data in a consistent and transparent manner. The infrastructure is capable of handling tens...
Coreform IGA is the world’s first fully spline based commercial simulation software that implements the Flex Representation Method, which allows users to setup and solve complex problems in science and engineering with less effort than traditional finite element analyses. Whereas many solvers may sacrifice accuracy or capabilities for the sake of model preparation simplicity, or may require intensive model preparation in order to solve challenging problems, Coreform IGA aims to provide world-class simulation capabilities coupled with simple model setup. Coreform IGA is actively advancing the state of spline based simulation technology. New features and capabilities are continually being added as they are developed. These new features may not be fully production ready, but they may be of interest to many...
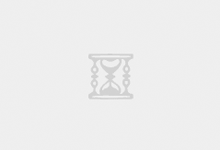
Coreform Flex harnesses Coreform’s patent-pending isogeometric analysis (IGA) technology to eliminate the need for meshing and defeaturing. Now, projects that used to take months can be accomplished in weeks or even days. Coreform Flex 2024.08 Tested Picture Coreform Flex updates include user experience enhancements, an improved Python interface, improved Flex meshing, new import/export capabilities to Coreform Flex Preprocessor, and the introduction of a number of beta features to Coreform Flex Solver. Read more.